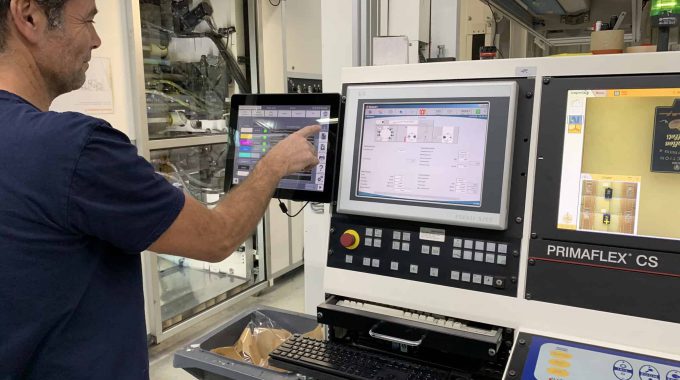
Estandarización de la viscosidad en la impresión flexográfica
Un nuevo enfoque para controlar la variable más grande en impresión flexográfica y de huecograbado
Introducción
En la historia de nuestra empresa hemos aplicado todo tipo de sensores de viscosidad: rotacional, de bola descendente, de pistón descendente y de onda acústica. La similitud entre estos sensores es que todos están calibrados con copa, en nuestro caso la copa DIN con salida de 4 mm. En sí mismo, esto funcionó bien y, debido a la falta de una alternativa mejor, la copa DIN 4 se convirtió en la medida estándar en la industria de la flexografía y el huecograbado. En diciembre de 2017, mientras buscaba una mejor solución, me puse en contacto con el Rheonics SRV como alternativa a los sensores que habíamos estado usando, que eran demasiado inexactos e insuficientemente repetibles. En enero de 2018 comenzamos a probar dos de estos sensores y en junio de 2018 equipamos las 8 estaciones de impresión de la prensa CI con Rheonics SRV. El año pasado realizamos muchas pruebas, reuniendo experiencia y nuevos conocimientos. Desarrollamos una fórmula para convertir la unidad centipoise, o mPaS, que es la unidad entregada por el SRV, a copa DIN de 4 segundos porque estábamos acostumbrados a trabajar con estas unidades. Después de unos meses decidimos dejar de utilizar por completo las unidades de copa DIN, por motivos que quedarán claros en este artículo.
La generación actual de máquinas de impresión es extremadamente precisa en términos de ajuste (en un rango de μm) y tiene un alto grado de automatización, como un sistema de inspección 100%, configuración de impresión totalmente automática de rodillos anilox y cilindros de placa, control de registro automático y Medición de color espectral en línea. Sin embargo, la variable más grande en el proceso de impresión, la viscosidad de la tinta, todavía se mide con una unidad que se determina manualmente. En muchos casos, incluso los controles automáticos de viscosidad se calibran con una taza porque los operadores están acostumbrados a pensar en segundos de taza. En la práctica, la calibración de la viscosidad a menudo no se realiza porque lleva mucho tiempo o porque las copas están sucias o no están disponibles.
La viscosidad es un parámetro muy importante en la calidad final del material impreso. Si la viscosidad no es correcta, el comportamiento del flujo y el grosor de la capa de tinta variarán, lo que provocará problemas en la calidad de impresión. Además, una viscosidad de tinta mal ajustada puede conducir a un consumo excesivo de tinta.
Exactitud
Todo operador está acostumbrado a trabajar con algún tipo de vaso medidor de viscosidad. Estas mediciones nunca han sido totalmente estandarizadas y solo son "confiables" en un rango de medición relativamente estrecho con un gran margen (5-10%) de error. Algunos de estos errores son causados por la taza en sí, otros son una función de la habilidad del operador. Las mediciones no son repetibles. La temperatura, que tiene una gran influencia en la viscosidad, es difícil de controlar. La contaminación de la copa y las diferentes densidades de tintas influyen en la velocidad de agotamiento. Todo esto se suma a una mala repetibilidad y precisión de las mediciones de copa DIN.
En la práctica, los márgenes de error pueden ser tan altos como 5-10%, que es un gran ancho de banda de viscosidad. Por ejemplo, para una tinta que tiene una viscosidad de 20 s, un margen de error entre 5-10% significa un ancho de banda entre 1 sy 2 s.
¿Cómo influye la precisión y repetibilidad de la Rheonics ¿SRV se compara con las medidas de la copa DIN?
Aquí hay un extracto del Rheonics Hoja de especificaciones SRV:
Rango de viscosidad | 0.4 a 250,000 + cP |
Precisión de viscosidad | 5% de lectura (estándar) 1% y mayor precisión disponible |
Reproducibilidad | Mejor que 1% de lectura |
Temperatura | Pt1000 (DIN EN 60751) |
Temperatura del fluido del proceso | -40 hasta 300 ° C (575 ° F) |
Temperatura ambiente | -40 hasta 150 ° C |
Rango de presión | hasta 7,500 psi (barra 500) |
El funcionamiento del sensor se basa en un elemento vibratorio que se encuentra sumergido en el fluido, y cuya resonancia es amortiguada por la viscosidad del fluido. El Rheonics SRV se diferencia de otros sensores de vibración en que su resonador está completamente equilibrado, lo que hace que su precisión sea inmune a su entorno mecánico. También es extremadamente robusto, lo que significa que se puede limpiar, cuando sea necesario, frotándolo con un trapo empapado en disolvente.
La especificación del fabricante muestra que tiene un amplio rango de medición y una precisión muy alta, pero ¿qué significa eso en la práctica? Probamos su precisión agregando 20 g de solvente a 25 kg de tinta. El sensor registró un cambio de viscosidad de 0.1 mPaS, que es el equivalente a una diferencia de medición de taza de 02 segundos. Esta es una precisión previamente desconocida de la medición de la viscosidad en esta industria. Y debido a que el SRV incorpora una medición de temperatura precisa en el elemento sensor, es posible compensar con precisión los efectos de la temperatura, como describiremos en la siguiente sección.
Hemos descubierto que trabajar con la copa no solo está desactualizado, sino que también es contraproducente. Después de unos meses, dejamos de convertir la viscosidad de mPa.s a segundos, finalmente elevando la medición de viscosidad, la última variable crucial en la impresión, al mismo nivel tecnológico que el resto del proceso. Finalmente llegamos al siglo 21st.
Comportamiento no newtoniano, tixotropía y viscosidad compensada por temperatura
Debido a la precisión y repetibilidad de la Rheonics Sensor SRV, hemos obtenido mucha información sobre el comportamiento de las tintas, a veces más de lo que esperábamos. La tinta es un medio reológicamente complejo y el SRV nos da una idea de esa complejidad que no es observable con la copa DIN.
Las tintas basadas en solventes exhiben un comportamiento no newtoniano. Bajo la influencia de la fuerza de corte, su viscosidad cambia. La tinta también es tixotrópica, una tinta estacionaria que tiene una viscosidad apreciablemente diferente que una tinta que está en movimiento. ¡La viscosidad de una tinta estacionaria puede diferir de la de una tinta en movimiento hasta en un 20%! Y además, la viscosidad de la tinta depende en gran medida de la temperatura. En las prensas de impresión en las que la temperatura de las tintas no está condicionada, la temperatura de la tinta, y por lo tanto la viscosidad, puede variar mucho debido a los cambios en la temperatura ambiente, pero también debido a la generación de calor en la prensa. Una de las primeras cosas que hemos explorado con el SRV de Rheonics es la dependencia de la temperatura de la viscosidad de la tinta.
Construimos una configuración de prueba que consiste en un circuito de flujo cerrado en el que la tinta se bombea continuamente en un circuito, a una velocidad comparable a la del circuito de tinta en nuestra prensa, y se calienta lentamente. Cada segundo se miden la temperatura y la viscosidad, lo que da más de mil puntos de medición en una ejecución de prueba típica.
El gráfico de la Fig. 1 muestra la dependencia de la temperatura de la viscosidad de varias tintas diferentes (tinta de nitrocelulosa modificada amarilla, magenta, plata y un blanco de poliuretano) en un rango de temperatura de 20 ° C. En este rango, la viscosidad puede diferir hasta un 60%.
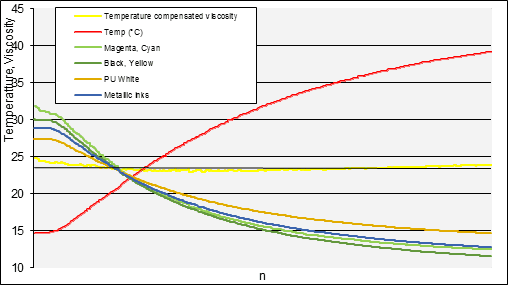
Figura 1. Dependencia de la temperatura de la viscosidad de la tinta.
Uno de los usos más importantes de la medición de la viscosidad es determinar cuándo y cuánta tinta debe diluirse para compensar la pérdida de solvente durante el proceso de impresión. La evaporación del solvente aumenta la carga de pigmento de la tinta, lo que resulta en una mala calidad de impresión y un consumo excesivo de tinta. Esta pérdida de disolvente también aumenta la viscosidad de la tinta. Sin embargo, dado que la viscosidad también es una función importante de la temperatura, es necesario distinguir entre los efectos de la temperatura y la evaporación para determinar la cantidad y el momento de la adición del solvente.
Sin compensación de temperatura, una tinta a baja temperatura daría una lectura de alta viscosidad, lo que sugiere que la dilución es necesaria. Sin embargo, diluir la tinta daría una densidad de color más baja, ya que la mayor viscosidad se debía a una temperatura más baja, no a una mayor carga de pigmento.
Usando gráficos como los de la Fig. 1, desarrollamos un algoritmo que nos permite compensar el efecto de la temperatura sobre la viscosidad, lo que resulta en una "viscosidad compensada por temperatura" que es una medida real de la carga de pigmento. Por lo tanto, se puede usar directamente para controlar la adición de solvente para compensar la evaporación, ya que elimina la temperatura como una variable que afecta la medición.
Usando nuestro algoritmo de compensación, reducimos la desviación del error al 1% en todo el rango de temperatura. En el control automático de viscosidad se puede seleccionar la compensación de temperatura para cada tipo de tinta. Hemos determinado esta curva para casi todas las tintas que utilizamos, y hemos determinado los parámetros de compensación de temperatura utilizando nuestro algoritmo especial, lo que nos permite finalmente lograr un control más estricto sobre la carga de pigmento y su efecto en la calidad de impresión.
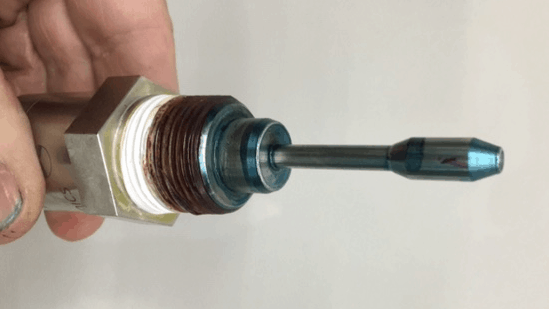
Figura 2. El sensor SRV después de la medición en tinta cian
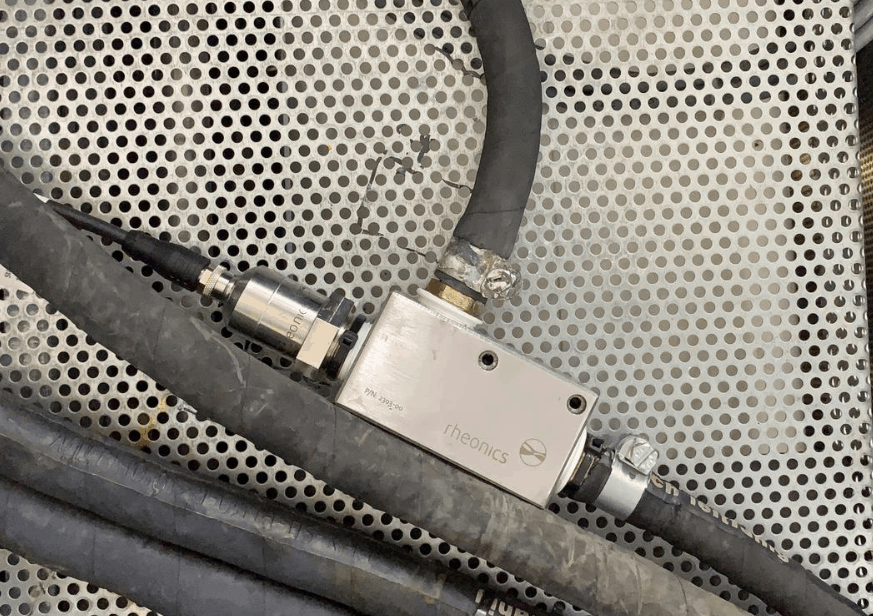
Figura 3. SRV instalado en la línea de tinta, que muestra Rheonics adaptador de impresión
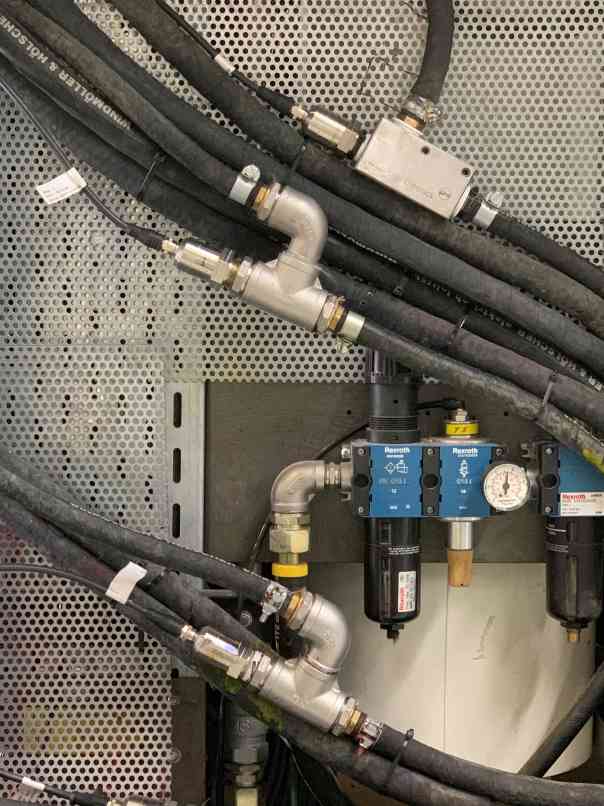
Figura 4. Cuatro SRV instalados en una prensa, usando tees de tubería simples como adaptadores
Instalación
El sensor está montado en un conector con una abertura de entrada y salida e instalado en la línea de suministro entre la bomba de tinta y la cámara doctor blade. Las influencias tales como las vibraciones de la máquina o las pulsaciones de presión de la bomba de diafragma no tienen ningún efecto sobre el funcionamiento del sensor o la precisión de la medición.
El sensor no requiere mantenimiento: cada ciclo de limpieza de las líneas y la cámara aseguran que el sensor esté limpio nuevamente, ya que se lava automáticamente en solvente. Como se muestra en la Fig. 2, solo puede quedar una capa de color muy delgada en el sensor, lo que no tiene influencia en su precisión o repetibilidad. Y debido a la construcción robusta del sensor, cualquier limpieza necesaria se puede hacer con un trapo empapado en solvente, sin peligro de dañar el sensor o cambiar su calibración.
Todos los sensores están conectados por separado mediante cables de grado industrial a sus unidades electrónicas, y éstas se comunican con una computadora de grado industrial. La computadora controla una isla de válvulas, que a su vez controla las válvulas accionadas neumáticamente para dosificar solvente. El sistema incluye una pantalla táctil, junto al panel de control del operador, que opera la interfaz de usuario intuitiva del Rheonics Software de control de viscosidad, Inksight. En la creación de la interfaz de usuario era obvio que debía ser clara, intuitiva, eficaz y rápida de utilizar. La interfaz muestra un panel de control en el que el operador puede controlar la viscosidad de todas las estaciones. Los controles sensibles al tacto permiten al operador encender o apagar estaciones individuales, habilitar el control automático y establecer los límites de viscosidad. Un centro de estación separado cambia a una pantalla que monitorea la viscosidad a lo largo del tiempo y permite el ajuste de sensores y válvulas específicos.
Además, el software notifica al operador cuando los cambios de viscosidad son demasiado grandes y ayuda haciendo la corrección correcta para resolver el problema.
Control automático, CS-Control
Durante la impresión se produce una evaporación continua de los disolventes; la evaporación aumenta al aumentar la velocidad de impresión y la temperatura de la tinta. Los sensores SRV miden el valor real de la viscosidad y la temperatura de la tinta una vez por segundo, lo que permite al software calcular la viscosidad con compensación de temperatura. Esto, a su vez, permite al controlador determinar si la viscosidad compensada por temperatura cae dentro de la tolerancia deseada. El controlador agregará una cantidad de solvente que depende del tamaño de la desviación del punto de ajuste. Durante la impresión, es posible mantener una desviación de solo un 0.5% del punto de ajuste. Se utilizan válvulas dosificadoras especiales que pueden agregar las cantidades muy pequeñas de solvente que son necesarias para lograr un control tan fino. Las siguientes gráficas son del mismo color con diferentes escalas, con líneas verticales magenta que indican la dosificación automática de disolvente.
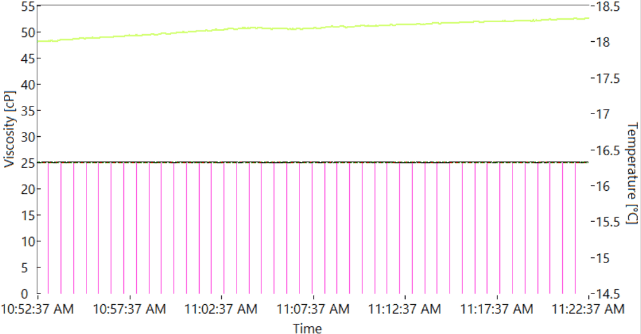
Figura 5a. Temperatura compensada viscosidad y temperatura vs. tiempo, escala vertical gruesa
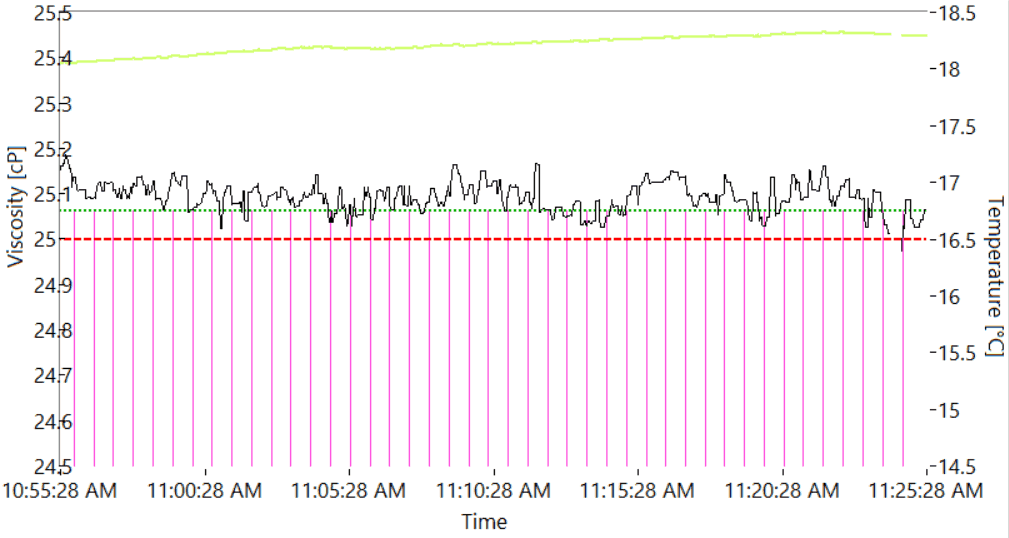
Figura 6b. El mismo diagrama que el anterior, con escala vertical expandida. La variación de la viscosidad compensada por temperatura es menor que 0.2 mPaS
El sistema de control basado en SRV es extremadamente preciso porque puede compensar rápida y frecuentemente la evaporación que ocurre constantemente durante el proceso de impresión. Para lograr desviaciones tan pequeñas del punto de ajuste, el sistema a veces dosificará tan poco como 10 g de solvente cada treinta segundos.
Si se agrega una tinta con una viscosidad demasiado alta al cubo de tinta, el control responde inmediatamente midiendo la respuesta a cada dosis de disolvente, y la dosificación posterior del disolvente se ajusta en consecuencia. Al final, el punto de ajuste se alcanza muy gradualmente con muy poco sobreimpulso. Además del control extremadamente preciso, es posible mantener la viscosidad estable cuando el nivel en el depósito de tinta es muy bajo, lo suficiente como para bombear la tinta a través del sistema.
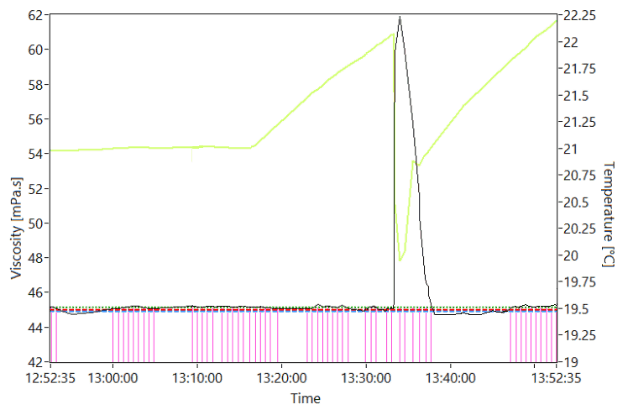
Figura 6. Respuesta del sistema a la adición de un gran volumen de tinta fría a un sistema que funciona a 21 deg. C. Observe el rápido tiempo de recuperación de la viscosidad compensada por temperatura.
Garantía de calidad, mejora y estandarización.
Un operador experimentado sabe qué viscosidad debe mantenerse para qué tipos de tinta en el proceso particular que se utiliza. Esto depende del tipo de tinta: el color Pantone, así como desafíos especiales, como los que presentan las tintas metálicas y blancas, que tienen un comportamiento algo diferente con la temperatura que las tintas "normales". Y la viscosidad deseada también depende del tipo de sustrato en el que se realiza la impresión.
Para comprender mejor el problema y su solución, realizamos una serie de experimentos sobre los efectos de la dilución de tinta en la calidad de impresión y la viscosidad de tinta medida. Con estos resultados, ahora sabemos qué viscosidades deben mantenerse para el tipo de sustrato (papel, poliéster, polietileno, polipropileno).
En un primer experimento, 10 kg de tinta se diluyó al 10%, la prensa corrió a 200 metros / min, se marcó la película de poliéster y se detuvo la prensa. La tinta se diluyó con un 3% adicional de disolvente, la tinta se hizo circular hasta que la viscosidad se estabilizó y el proceso se repitió un total de 15 veces. Se retiró la película y se midieron todos los segmentos 15 con un espectrofotómetro, y se hicieron fotografías de los segmentos de la película para una evaluación visual subjetiva.
La siguiente figura compuesta muestra la apariencia visual de la calidad de impresión en una serie de diluciones.
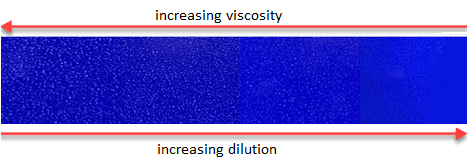
Figura 7. Variación de densidad de color con dilución de tinta y viscosidad.
En la dilución más baja (viscosidad más alta), se deposita demasiada tinta y no fluye correctamente. Se desarrollan pequeños agujeros y la calidad general es deficiente. Aunque el color entre los agujeros es bastante denso, la densidad medida es baja, debido a la alta reflectividad de los poros. A medida que aumenta la dilución, la viscosidad disminuye y el flujo mejora, pero la carga de pigmento disminuye y el color se vuelve más claro. Cada muestra se midió con el espectrofotómetro y se comparó con la referencia digital PMS. La siguiente gráfica y tabla muestran el dE2000 y la densidad de color como funciones de dilución y viscosidad. Los valores de diferencia de viscosidad se refieren a la muestra 6, que es la densidad objetivo.
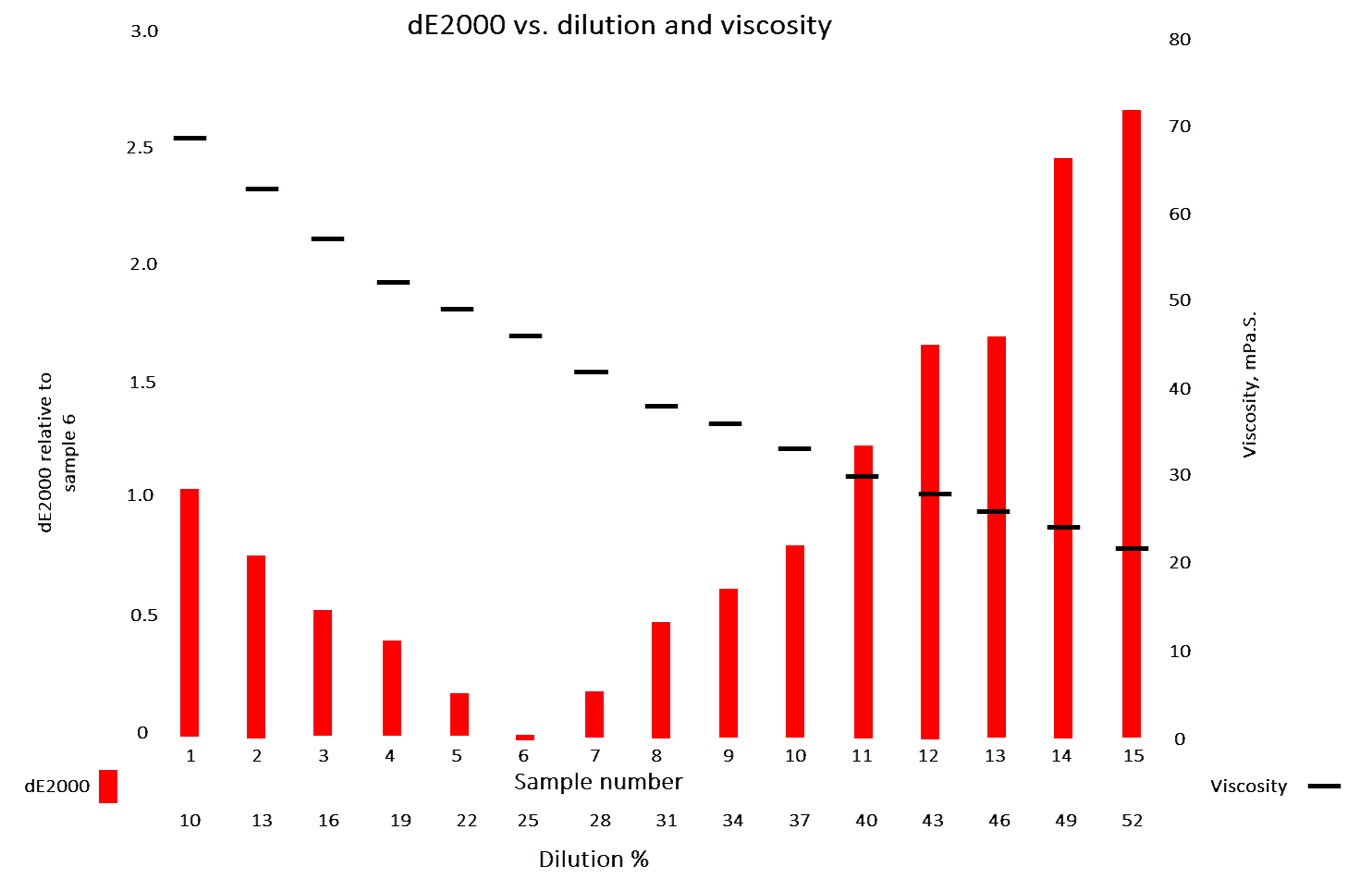
Figura 8. Densidad del color en función de la dilución y densidad de la tinta. Los valores de dE2000 se refieren a la muestra 6
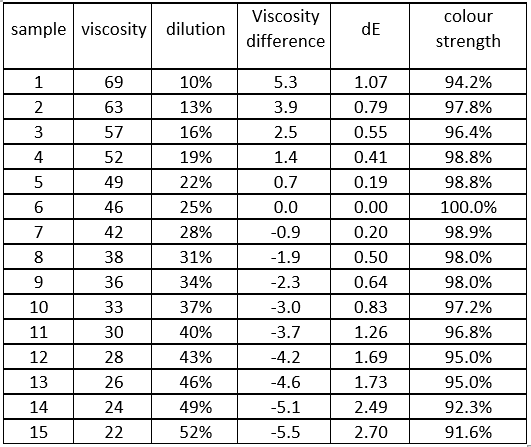
Tabla-1. Valores numéricos de dE2000 y fuerza de color frente a dilución. La diferencia de viscosidad es relativa a la muestra 6
Este experimento muestra que con el Rheonics sistema, se puede lograr un control de viscosidad muy preciso, con un ancho de banda de viscosidad del 0.5%. Al dosificar cantidades muy pequeñas de disolvente aproximadamente cada 30 segundos, el sistema permite lograr variaciones muy pequeñas en los valores de dE.
En el momento en que se realizaron estos experimentos, el ancho de banda de viscosidad habitual era de ± 0.5 tazas segundos (aproximadamente ± 2.2 mPaS), comprobándose la viscosidad cada 5-10 minutos. La cantidad de solvente que se dosificó fue entre 0.2 y 0.5 kg (dependiendo de la cobertura de tinta, tipo de solvente, volumen del anilox, velocidad de la máquina y temperatura.
Ahora hemos cambiado el proceso de impresión de un color Pantone, porque no sólo sabemos qué viscosidades deben mantenerse para el tipo de sustrato, sino que también podemos mantener tolerancias estrictas en esta viscosidad. Ciertos sustratos requieren una mayor viscosidad debido al hecho de que la tinta "se hunde" demasiado y, por lo tanto, la estructura se vuelve visible, lo que resulta en una disminución de la intensidad del color, mientras que otros sustratos necesitan una viscosidad menor debido a su superficie lisa y buena aceptación de la tinta. Con la experiencia adquirida con el Rheonics sabemos exactamente qué viscosidad se debe mantener para el tipo de sustrato (polietileno, polipropileno, poliamida, poliéster, papel y biodegradable) y, de hecho, hemos determinado una estandarización por nosotros mismos.
Con la primera impresión, se mide la densidad de color del color pantone y luego el operador verifica si la tinta tiene la viscosidad correcta para el sustrato relevante. (Por lo general, la tinta no se lleva al valor correcto de antemano porque el sustrato puede variar ligeramente en términos de calidad de la superficie, por lo que tenemos espacio para jugar con la viscosidad para obtener resultados óptimos).
En el método anterior, si un color tenía una densidad de color demasiado alta, lo redujimos con barniz y / o con un rodillo de anilox diferente. En caso de duda, la viscosidad se verificó con una copa, que generalmente requería una recalibración del sensor correspondiente.
Debido a que ahora tenemos una medida más confiable para la viscosidad de la tinta con compensación de temperatura inicial, su viscosidad se puede ajustar de forma automática diluyendo una tinta al valor correcto. Debido a que se mantienen los valores correctos de viscosidad, esto conduce a una mejor transferencia de tinta del rodillo anilox a la plancha de impresión y finalmente al sustrato. La contaminación del rodillo anilox también se puede notar antes porque sabemos qué intensidad de color se debe alcanzar con una cierta viscosidad.
Una viscosidad demasiado alta conduce a una transferencia deficiente que resulta en características visuales como opacidad y "efecto fantasma". Debido a una viscosidad más precisa, la celda del rodillo anilox se vacía mejor y la tinta generalmente fluye mejor, dando una capa de tinta más suave y una mayor intensidad de color. Con el aumento de la velocidad, la transferencia de tinta disminuye, pero debido a que la tinta tiene la viscosidad correcta y funciona de manera óptima, estas variaciones son más pequeñas en comparación con nuestro método anterior que usa sensores calibrados en copa.
En los últimos seis meses hemos mejorado color, calidad y son capaces de mantener desviaciones mucho más pequeñas de los valores dE2000, especialmente. Un resultado de un control de la viscosidad más estricto es que el sistema de inspección de impresión detecta muchos menos errores en las desviaciones de la intensidad del color. Nuestros operadores tienen total confianza en los valores precisos y repetibles de los sensores y el sistema de control. Esta confianza ha llevado a nuestra prensa a lograr una excelente calidad de impresión para trabajos pequeños y grandes. Además, no hemos realizado mantenimiento ni calibración de los sensores y, más allá de nuestras mediciones iniciales de parámetros de viscosidad compensada por temperatura para cada tinta, no es necesario realizar una estandarización adicional de los valores de viscosidad. Ahora sabemos qué viscosidades deben mantenerse para sustratos específicos. Después de imprimir cada nuevo pedido, almacenamos los valores establecidos de viscosidad y los usamos para repetir pedidos del mismo trabajo.
Una desviación de 5% se aplica a un color y no al otro, creo que es mejor afirmar que podemos mantener los valores dE mucho mejor durante la impresión de un pedido y mantener el valor dentro de un ancho de banda mucho menor valor inicial.
Entonces, ¿por qué no convertir a segundos copa?
Aunque existen fórmulas para convertir los valores de viscosidad de mPaS a segundos de copa DIN, hemos descubierto que abandonar los segundos de copa tiene varias ventajas.
Sobre todo, ha cambiado la forma en que pensamos sobre la viscosidad. Mientras pensamos en términos de segundos de copa, mantener un control estricto sobre la viscosidad parecía una tarea imposible. Nuestras expectativas estaban limitadas por nuestras experiencias anteriores, por lo que establecimos un nivel más bajo de lo necesario para lograr el tipo de calidad de impresión que sabíamos que era alcanzable.
Además, pensar en términos de segundos copa nos hizo querer tomar una copa y verificar la precisión de estos nuevos sensores, con los que no estábamos familiarizados en ese momento. ¡Pero verificar la precisión de los sensores con un método mucho menos repetible puede dar la falsa impresión de que los sensores en sí mismos no son repetibles! Solo cuando comparamos los resultados de impresión reales con el nuevo sistema de sensores con lo que estábamos acostumbrados, vimos el valor real de pensar en las unidades nuevas y desconocidas. Nos permitió "pensar en pequeño", para poder ver pequeñas variaciones en la viscosidad que de otro modo serían invisibles. Además, nos permitió obtener nuestra viscosidad bajo un control más estricto, lo que tuvo un impacto positivo directo en la calidad de nuestro producto final, que es, después de todo, nuestro objetivo principal.
A medida que aumentan las velocidades de impresión y los márgenes de beneficio se reducen, “hacerlo bien a la primera” se vuelve mucho más importante. Un error en el ajuste inicial de la viscosidad puede provocar la producción de varios miles de metros de residuos en muy poco tiempo. Con el Rheonics Gracias al sistema SRV, hemos podido agilizar nuestro proceso de impresión y al mismo tiempo mejorar la calidad del color y reducir los residuos.
En el próximo artículo de esta serie.
En este artículo nos hemos centrado en el desafío básico del control de la viscosidad.oring y control, lo que demuestra el beneficio de un control estricto para la calidad de impresión y la economía de tinta. En el próximo artículo veremos más de cerca el sistema de control que permite al operador de la prensa lograr y mantener esta calidad con un mínimo de intervención. El sistema, Rheonics La solución de impresión (RPS) consta de una caja de control que contiene una computadora de proceso y un control de válvula que controla directamente la dilución del solvente según la viscosidad medida. El RPS puede acomodar hasta 10 estaciones de impresión, con sensores SRV realizando el monitoreo.oring. El hardware RPS está respaldado por un sofisticado sistema de software que estima la dilución requerida en función de la viscosidad medida y está controlado por una interfaz de usuario simple e intuitiva para configurar y ajustar la viscosidad deseada.
También consideraremos el desafío del control de la viscosidad de tintas especiales, como las tintas UV cuya viscosidad es muy sensible a la temperatura y cuya viscosidad se controla mejor a través de controles térmicos.